Jak produkuje się magnesy ferrytowe?
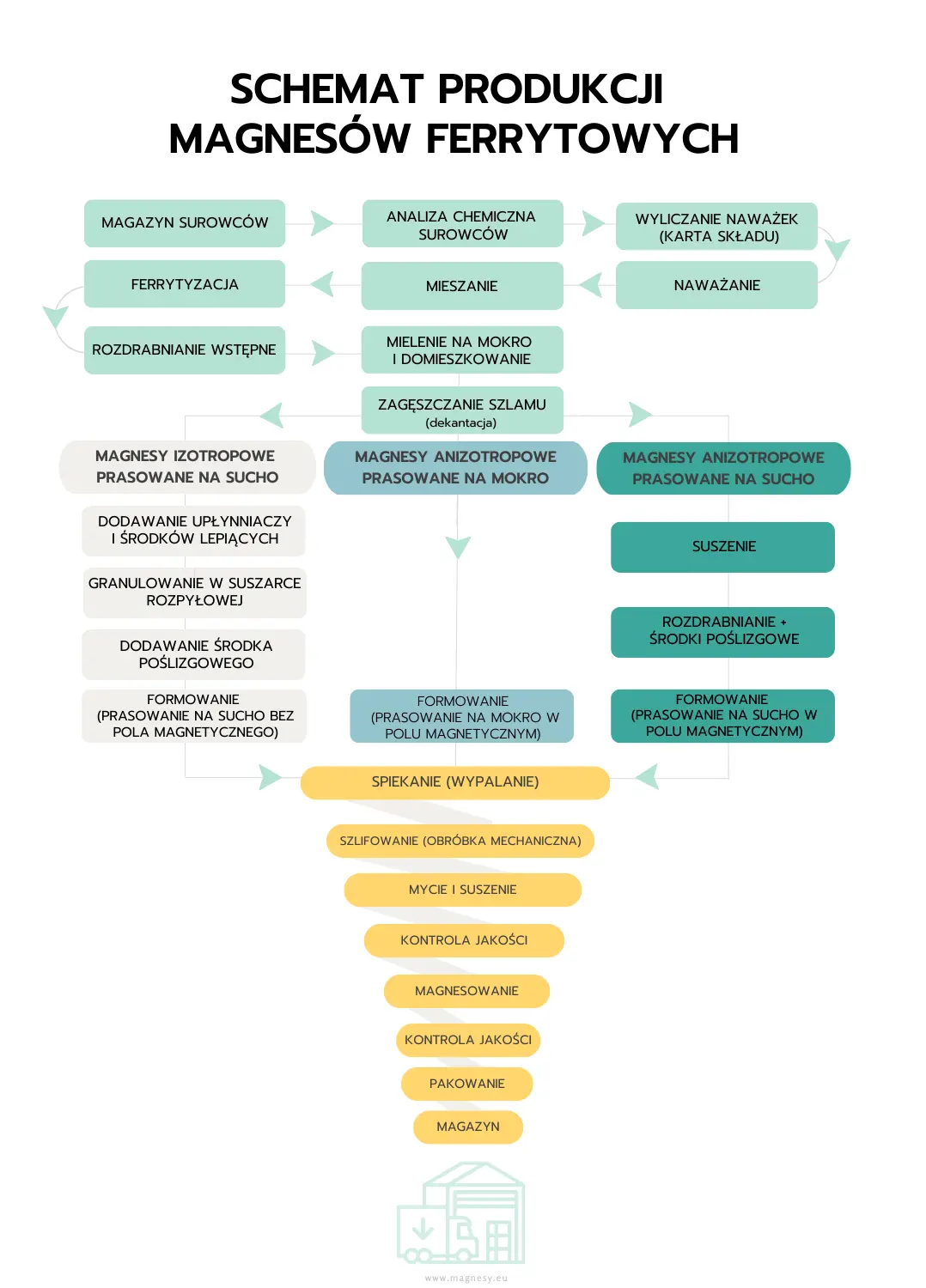
Zdj. 1. Skrócony schemat produkcji magnesów ferrytowych
Proces produkcji ferrytu baru i ferrytu strontu
Etapy:
- magazyn surowców
- analiza surowców
Należy ją wykonać gdy surowiec jest dostarczony bez atestu lub jest źle zapakowany, co może powodować zmianę jego wilgotności w trakcie transportu i przechowywania.
- wyliczanie naważek (karta składu)
Technolog wyliczający kartę składu (naważki poszczególnych surowców) uwzględnia czystość wyjściowych surowców jak również domiał żelaza w trakcie procesu mieszania i mielenia. W związku z tym, że mielniki i elementy mieszające systematycznie się zużywają, domiał żelaza ciągle się zmienia. Należy więc okresowo uzupełniać mielniki i wymieniać elementy mieszające. W zależności od projektowanych parametrów gotowych wyrobów odpowiednio ustala się temp. ferrytyzacji jak i czas przemiału.
- naważanie
- mieszanie
Mimo, iż mieszanie surowców na mokro połączone z mieleniem jest skuteczniejsze od mieszania na sucho to obniżenie kosztów produkcji i skrócenie procesu przesądziło o stosowaniu mieszania na sucho.
- ferrytyzacja w piecu
Ferrytyzacja odbywa się na ogół w piecach obrotowych o pracy ciągłej, ogrzewanych gazem. Nachylenie pieca wynosi około 3o do poziomu. Szybkość obrotu pieca 0,5-1,5 obr./min. Załadunek do pieca odbywa się od strony uniesionej i wypalany materiał przesuwa się w dół do końca pieca gdzie znajdują się palniki gazowe. Ustawienie temperatury wg. wskazań pirometru optycznego do około 1270oC ±20o. Spaliny gazu w piecu przemieszczają się przeciwbieżnie do ruchu wypalanego materiału ogrzewając go wstępnie.
W trakcie wypalania w piecu mieszaniny surowców następuje rozkład węglanu i proces tworzenia się ferrytu o strukturze heksagonalnej.
Ferrytyzacja ma na celu oddzielenie procesu powstawania ferrytu od procesu zagęszczania i rozrostu ziaren w procesie spiekania gotowych wyrobów, co znacznie poprawia parametry magnetyczne magnesów.
- rozdrabnianie
Powstały ferryt po wyjściu z pieca jest w postaci bardzo twardych i porowatych brył o nieregularnym kształcie i różnej wielkości. Przed przekazaniem go do dalszego etapu produkcji podlega rozdrobnieniu na kruszarkach szczękowych, walcowych i młynach bębnowych o pracy ciągłej do wielkości ziarna ˂ 0,5 mm.
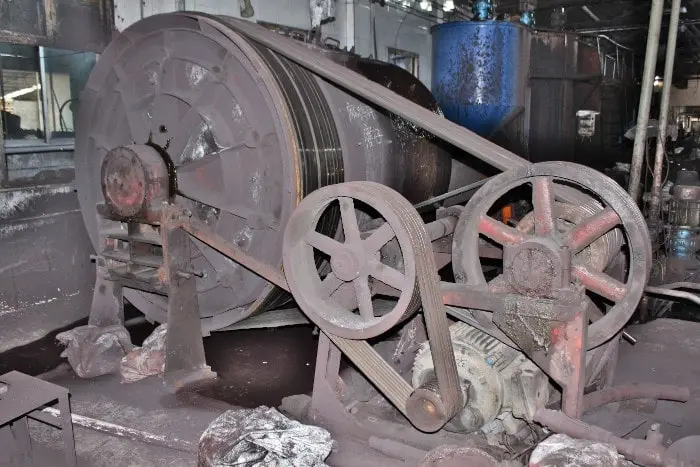
Zdj. 2. Młyn kulowy do mielenia surowców na magnesy ferrytowe
Przygotowanie szlamu, proszku i granulatu ferrytowego do formowania magnesów ferrytowych
Przygotowanie szlamu:
- naważanie proszku ferrytowego i domieszek
Naważanie proszku ferrytowego odbywa się na wagach o zakresie ~150 kg i dokładności 0,1 kg. Domieszki naważane są na wagach o dokładności 0,1 g. Jako domieszki stosuje się najczęściej: SiO2, Al2O3, CaCO3 a czasem bentonit. Dodając domieszki w odpowiednich ilościach można regulować rozrost ziaren w gotowym wyrobie jak i jego gęstość końcową i co za tym idzie końcowe parametry magnetyczne. W praktyce technolog wypisując kartę składu podejmuje decyzję o przebiegu procesu technologicznego i przeznaczeniu (o parametrach końcowych) tej partii tworzywa.
- załadunek do młyna naważonych substancji i zalanie wodą
Najpierw wlewa się do młyna ~70% wody a następnie sypie się na raty sproszkowane materiały co chwila uruchamiając młyn. Na koniec uzupełnia się resztę wody i uruchamia młyn na określony czas pracy. Po około 30 minutach uruchamia się obieg zamknięty mielonego szlamu.
- mielenie do wielkości ziarna w zależności od potrzeb od 0,7 do 1,5 µm
- zlewanie zmielonego ferrytowego szlamu do odstojników zbiorczych (mieszadeł) w celu ujednorodnienia kilku przemiałów
- zagęszczanie szlamu (dekantacja) do gęstości ~ 2,2 kg/litr
- zatwierdzanie
Ujednorodniony i zagęszczony szlam poddawany jest zatwierdzeniu przed przeznaczeniem go do dalszej produkcji poprzez wykonanie próbnych magnesów i ich pomiar oraz wykonanie pomiaru wielkości ziarna. Okresowo wykonuje się też analizę chemiczną w celu ustalenia powtarzalności procesu. Ilość domielonego żelaza i wielkość ziarna informują o skuteczności przemiału i o jakości elementów mielących (kule stalowe i pręty mieszające ze stali Hadfielda)
Odpowiednio wykonany szlam może być wykorzystany do formowania na mokro magnesów anizotropowych oraz do przygotowania z niego proszku do formowania magnesów anizotropowych na sucho lub też do wykonania granulatu do formowania magnesów izotropowych.
Przygotowanie proszku do formowania magnesów anizotropowych na sucho:
- suszenie szlamu
- bardzo dokładne rozdrabnianie (na pył)
- dodawanie środka poślizgowego np. stearynianu magnezu
- dokładne wymieszanie
W celu uzyskania lepszych parametrów magnesów magnesuje się szlam przed suszeniem. Po wysuszeniu proszek z magnesowanego szlamu nie musi być tak bardzo dokładnie rozdrabniany jak proszek ze szlamu niemagnesowanego. Tak jak w poprzedniej metodzie należy dodać środek poślizgowy.
Do wykonania takiego proszku można wykorzystać uszkodzone „braki miękkie” czyli wypraski magnesów anizotropowych formowanych na mokro.
Przygotowanie granulatu na magnesy izotropowe:
Granulat na magnesy izotropowe wykonuje się również ze szlamu po przemiale i dekantacji. W zależności od przeznaczenia można go wykonywać na suszarce rozpyłowej (wyroby małe i cienkościenne) oraz starą metodą sitową na wyroby duże (grubościenne).
Metoda granulowania „suszarkowa”
Przed podaniem szlamu na suszarkę rozpyłową dodaje się do mieszadła ze szlamem upłynniacz, środek wiążący oraz odpieniacz. Po wymieszaniu szlamu z dodatkami suszy się go w suszarce rozpyłowej a uzyskany granulat mieszany jest ze środkiem poślizgowym.
Tak uzyskany granulat odpowiednio oznaczony przeznaczony jest do formowania magnesów.
Metoda granulowania „sitowa”
- suszenie szlamu
- rozdrabnianie wstępne
- przecieranie przez sito o boku oczka ~ 0,6 mm
- mieszanie z wodnym roztworem polialkoholu winylowego
- prasowanie wstępne ~ 300kG/cm2
- rozdrabnianie wstępne
- przecieranie przez sito o boku oczka ~ 0,8 mm
- bębnowanie do utworzenia ładnej granulki
- odsiewanie pyłku na sicie o boku oczka ~0,2 mm
- suszenie do wilgotności 0,7%
- bębnowanie granulatu ze środkiem poślizgowym (stearynian-Mg)
Gotowy, odpowiednio opisany granulat przechowywany jest w szczelnych pojemnikach.
Formowanie
Formowanie magnesów anizotropowych na mokro w polu magnetycznym
Do tej operacji stosuje się prasy hydrauliczne (ręczne, półautomatyczne i automatyczne). Wybór prasy zależy od zapotrzebowania na poszczególne magnesy.
Każda z tych pras wyposażona jest w cewkę, która jest źródłem pola magnetycznego w trakcie formowania. Wewnątrz cewki znajduje się forma jednokrotna lub wielokrotna. Obudowa formy wykonana jest ze stali niemagnetycznej a matryce z niemagnetycznych węglików. Natomiast stemple górny i dolny wykonane są ze stali magnetycznie miękkiej. Górny stempel wyposażony jest w sitko okryte płótnem filtracyjnym. W trakcie formowania (prasowania) górny stempel opiera się na obudowie (zamyka formę). Dolny stempel cały czas jest nieruchomy. Wysokość uniesienia czoła matrycy od powierzchni stempla dolnego ustala pojemność matrycy a co za tym idzie wysokość wypraski. Gęstość wypraski wynosi około 2,85 g/cm3.
Kolejność operacji w automatycznym cyklu formowania na prasie hydraulicznej:
- otwarcie matrycy i odsłonięcie kanałów zalewowych
- stempel górny mocno zamyka matrycę opierającą się na jej obudowie
- włączenie pola magnetycznego, którego koncentracja powstaje w szczelinie między stemplem górnym i dolnym. Pole to bardzo skutecznie orientuje ziarna ferrytu we wtryskiwanym szlamie do formy.
- wtryskiwanie szlamu do matrycy (wtryskiwanie ustaje z chwilą osiągnięcia ustawionego ciśnienia)
- prasowanie – odbywa się poprzez spychanie matrycy przez stempel górny. Zsuwając się w dół po stemplu dolnym zamknięte zostają kanały dolotowe szlamu. Poprzez sitko w stemplu górnym próżnia wysysa ze szlamu wodę. Zmniejszająca się szczelina między stemplami powoduje wzrost w niej natężenia pola magnetycznego. Prasowanie ustaje po osiągnięciu ustawionego ciśnienia.
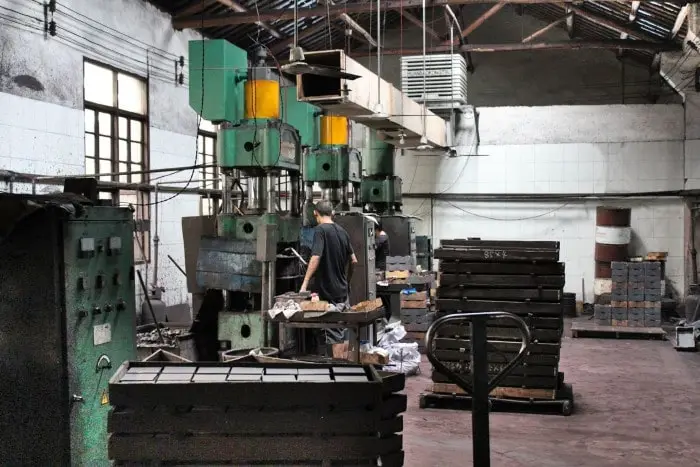
Zdj. 3. Proces prasowania magnesów ferrytowych
- magnesujące pole magnetyczne zostaje wyłączone a włącza się na chwilę zmienne pole rozmagnesowujące wypraskę.
- po rozmagnesowaniu wypraski stempel górny unosi się a matryca zsuwa się w dół do płaszczyzny stempla dolnego.
- odsłonięte wypraski zabiera chwytak podciśnieniowy na przenośnik taśmowy
- suszenie wyprasek
Formowanie magnesów anizotropowych na sucho w polu magnetycznym
Tą operację wykonuje się na prasach mechanicznych w systemie automatycznym lub półautomatycznym.
Specjalnie przystosowane prasy mają w stemplu górnym regulowaną poduszkę powietrzną a ruch stempla górnego umożliwia wykonywanie tzw. odpowietrzenia co zapobiega powstawaniu w wypraskach rozwarstwień. Operacje formowania są zbliżone do operacji prasowania magnesów na mokro. Różnica polega na tym, że proszek zasypywany jest do matrycy od góry przy uniesionym stemplu górnym. Proszek do matrycy zasypywany jest przez szufladkę, która napełniana jest w pozycji tylnej z leja zasypowego. Te wypraski są suche więc mogą być transportowane bezpośrednio do pieca. Gęstość tych wyprasek wynosi około 2,65 g/cm3.
Formowanie magnesów izotropowych bez udziału pola magnetycznego
Magnesy izotropowe formuje się najczęściej na wydajnych prasach mechanicznych w systemie automatycznym.
Granulat z leja zasypowego podawany jest szufladką do komory formy. Po wycofaniu się szufladki następuje zejście stempla górnego do komory matrycy i zaprasowanie kształtki.
Po osiągnięciu właściwego nacisku (lub pozycji) prasowanie ustaje i następuje odejście stempla górnego oraz obciągnięcie matrycy do poziomu górnej powierzchni dolnego stempla. Następnie szufladka zasypowa spycha wypraskę i pozostaje w tej pozycji do otwarcia matrycy, którą ponownie zasypuje.
Wypraski mogą być spiekane bezpośrednio po wyprasowaniu. Gęstość wyprasek wynosi około 3 g/cm3.
Spiekanie magnesów ferrytowych
Spiekanie magnesów ferrytowych odbywa się w piecach tunelowych o pracy ciągłej. W piecach tych jest możliwość regulacji kształtu krzywej temperaturowej: czyli wzrostu temperatury, długości szczytu i kształtu krzywej studzenia. Piece te również mają regulowaną szybkość przesuwu płyt nośnych wzdłuż pieca co ma zasadniczy wpływ na czas przebywania wyrobów w ustawionych temperaturach. Dobre piece mają bardzo małą różnice temperatur wzdłuż szerokości pieca co sprzyja dużej jednorodności wsadu, a co za tym idzie parametrów mechanicznych i magnetycznych spiekanej partii wyrobów.
Krzywa temperaturowa spiekania magnesów charakteryzuje się w miarę liniowym wzrostem temperatury, krótkim szczytem i dość szybkim studzeniem.
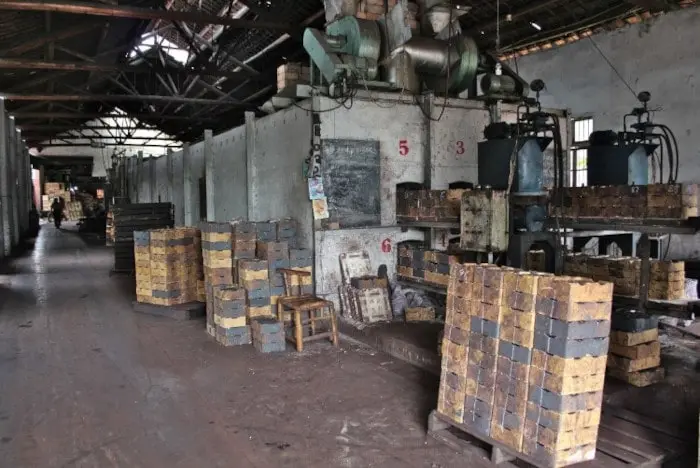
Zdj. 4. Piec tunelowy do spiekania magnesów ferrytowych
Obróbka mechaniczna spieczonych magnesów ferrytowych
Proces formowania i spiekania magnesów ma za cel wyprodukować je o wymiarach zbliżonych do ostatecznie potrzebnych. Udaje się to najlepiej przy produkcji niektórych magnesów izotropowych, dla których ostateczne wymiary mieszczą się w założonych tolerancjach i ich powierzchnie spełniają wymagania odbiorcy.
Wyroby nie spełniające wymagań pod względem jakości powierzchni jak i gabarytów podlegają obróbce mechanicznej.
Obróbka mechaniczna polega na szlifowaniu powierzchni magnesów tarczami i frezami diamentowymi przy intensywnym chłodzeniu wodą. Nie chłodzone magnesy w trakcie obróbki pękają (są słabym przewodnikiem ciepła). Woda chłodząca ułatwia szlifowanie wypłukując urobek z obrabianych magnesów. Płaszczyzny szlifowane są na szlifierkach do płaszczyzn o pracy okresowej lub ciągłej. Zewnętrzne powierzchnie cylindryczne obrabiane są na szlifierkach do wałków. Wewnętrzne powierzchnie cylindryczne szlifowane są na szlifierkach do otworów.
Natomiast magnesy segmentowe obrabiane są na specjalnie do tego celu wykonanych szlifierkach o pracy ciągłej. Takie szlifierki mają na swoim torze dwa zestawy tarcz. Pierwszy zestaw szlifuje końce łuków segmentów, natomiast drugi zestaw tarcz szlifuje powierzchnie łuku zewnętrznego i wewnętrznego jednocześnie. Za zestawami tarcz szlifierskich znajdują się myjka i suszarka.
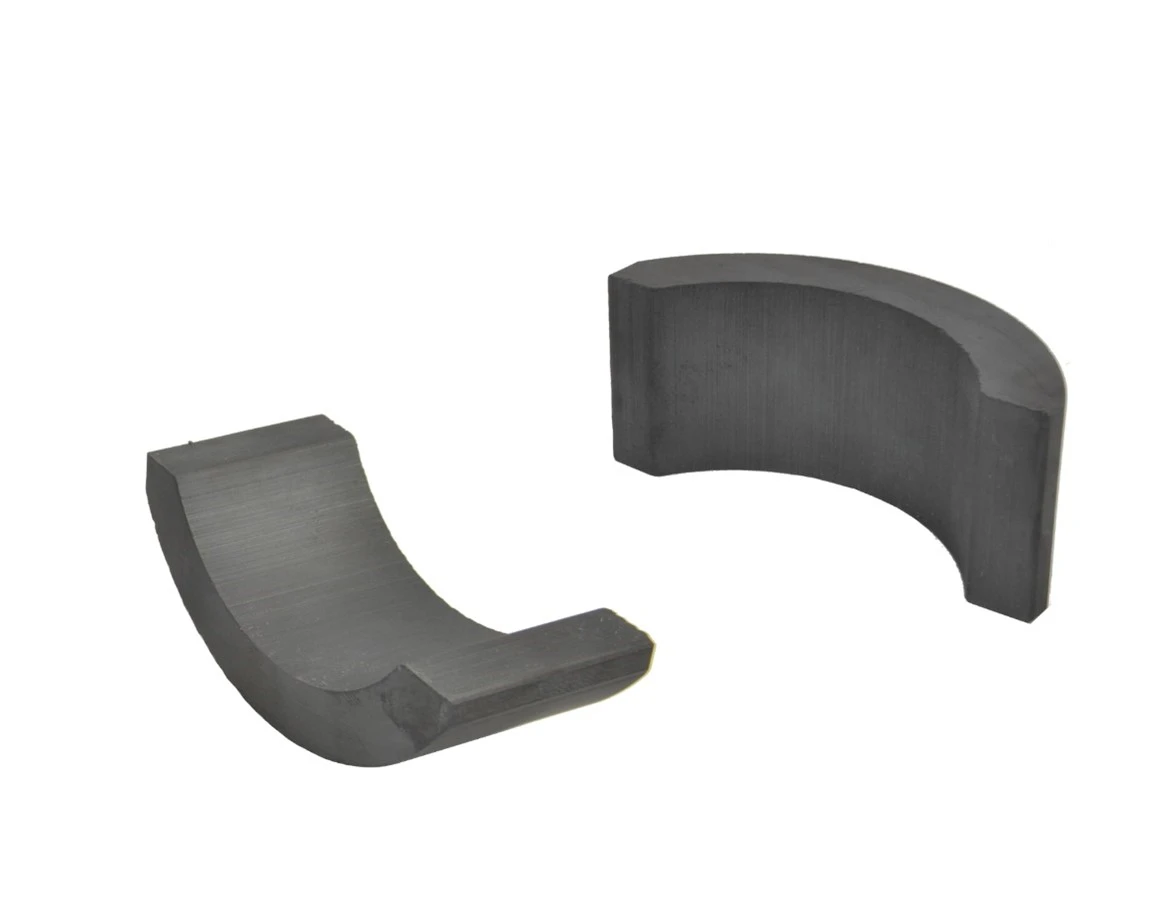
Zdj. 5. Przykładowe magnesy segmentowe
Mycie
Mycie odbywa się na ogół w myjkach taśmowych, które mają zestawy dysz od góry i od dołu, którymi na magnesy kierowana jest woda pod dużym ciśnieniem. Taśmy myjki wykonane są z siatki kwasoodpornej.
W drugiej strefie siatkowego taśmociągu myjki znajdują się intensywne nawiewy powietrza, które bardzo skutecznie suszą umyte magnesy.
Wyroby nietypowe i produkowane w mniejszych ilościach myte są ręcznie.
Magnesowanie
Magnesy anizotropowe magnesowane są zgodnie z ich wyróżnionym w procesie formowania łatwym kierunkiem magnesowania. Do wielu zastosowań potrzebne są magnesy, które mają więcej niż jedną parę biegunów.
Magnesy izotropowe nie mają wyróżnionego kierunku łatwego magnesowania i dlatego można je magnesować w dowolnym kierunku a także wielobiegunowo w zależności od potrzeb.
Do magnesowania używa się magneśnic jarzmowych lub impulsowych. Niektóre konstrukcje obwodów do magneśnic impulsowych umożliwiają pracę ciągłą (automatyczną). Do magnesowania wielobiegunowego wykonuje się specjalne obwody magnetyczne.
Wielu odbiorców produkujących silniki czy prądnice posiada własne obwody magnetyczne. Montaż nienamagnesowanych magnesów jest znacznie prostszy.
Gotowe wyroby przekazywane są do magazynu.
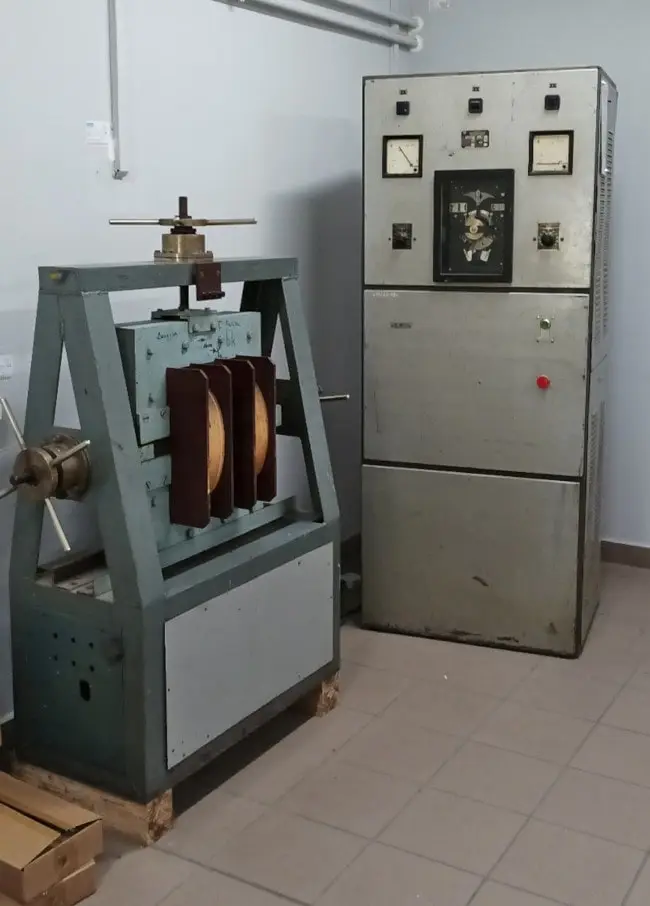
Zdj. 6. Magneśnica
Kontrola jakości magnesów ferrytowych
Kontrola jakości odbywa się w praktyce na każdym etapie produkcji ale najważniejsza jest wykonywana po myciu i po magnesowaniu.
Autor: Witalis Marek Zientek - pracował jako technolog oraz kierownik Wydziału Produkcji Doświadczalnej w Zakładzie Materiałów Magnetycznych „Polfer” mieszczącym się kiedyś na ul. Dzielnej w Warszawie. Oprócz magnesów ferrytowych Polfer produkował także miękkie magnetycznie rdzenie ferrytowe, oraz w małych ilościach wiązane magnesy neodymowe na bazie amerykańskiego proszku. Autor artykułu był także technologiem w firmie Wytwórnia Magnesów Renata i Elżbieta Zientek s.c. mieszczącej się kiedyś w podwarszawskich Jankach, produkującej magnesy ferrytowe formowane na sucho.
Marzec 2023 r. Stare Babice