Jak produkuje się magnesy neodymowe?
Proces produkcji magnesów neodymowych podzielony jest na wiele głównych etapów, oraz liczne etapy podrzędne. W produkcji wysokiej jakości magnesów neodymowych każdy krok jest bardzo ważny i ma znaczenie w osiągnięciu docelowo magnesów, o sprecyzowanych właściwościach fizycznych, chemicznych, a przede wszystkim magnetycznych.
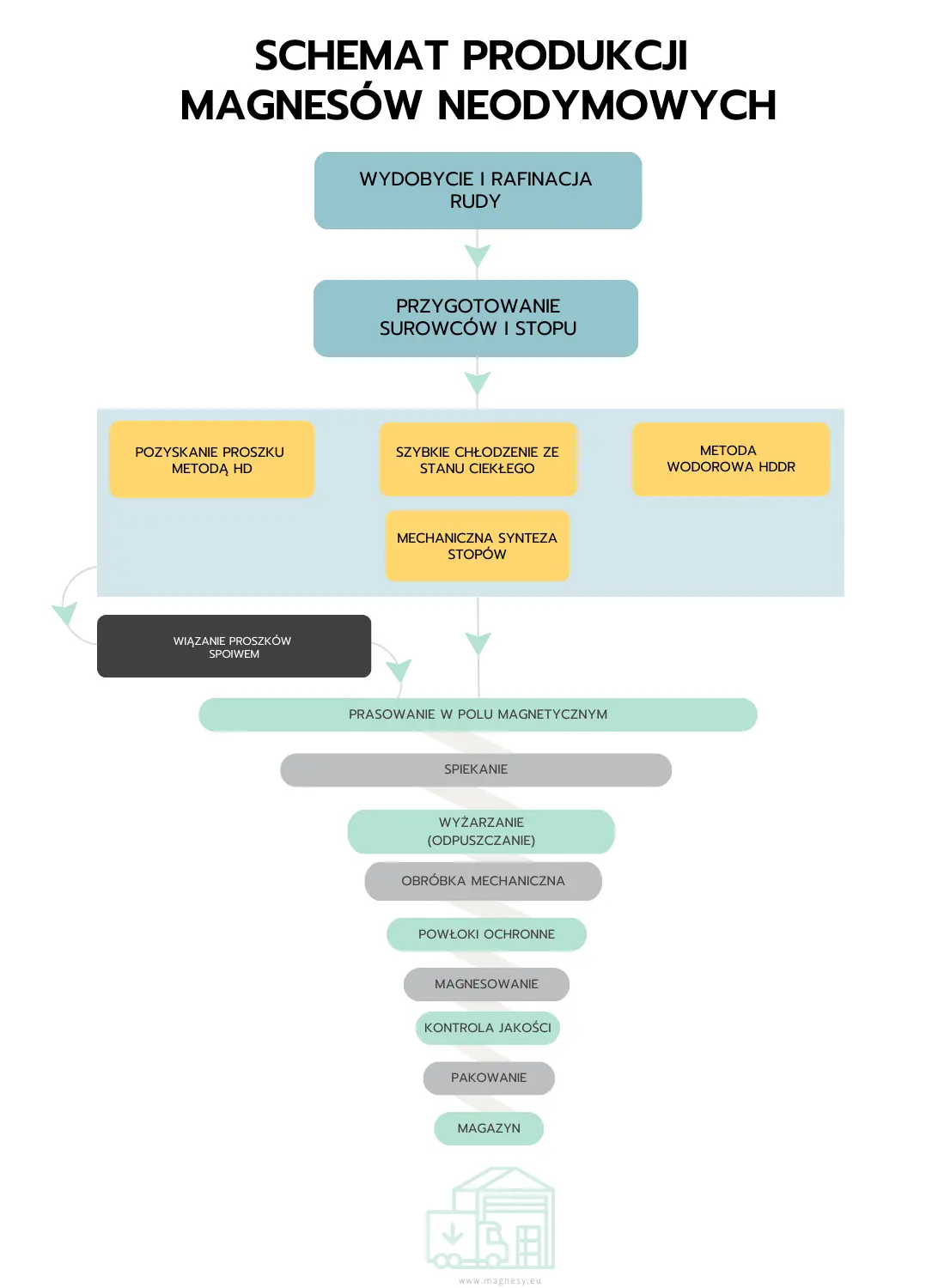
Rys. 1 Skrócony schemat produkcji magnesów neodymowych
Produktem wyjściowym do otrzymywania magnesów neodymowych jest stop neodymu, żelaza i boru. W wyniku różnych procesów rozdrabniania otrzymuje się proszek metaliczny, o takim samym składzie chemicznym, który stanowi materiał wyjściowy do formowania magnesów neodymowych. Powstały związek Nd2Fe14B tworzy tetragonalną strukturę krystaliczną. Neodym będący metalem ziem rzadkich stanowi kluczowy składnik stopu, pozwalający osiągnąć odpowiednie właściwości magnetyczne.
Wydobycie, przetwarzanie i rafinacja rudy
Większość kopalni metali ziem rzadkich to kopalnie odkrywkowe, w których po odkryciu warstwy wierzchniej wydobywa się rudę.
Po wydobyciu rudy ziem rzadkich jest ona kruszona i mielona. Następnie przechodzi proces flotacji, w którym jest mieszana z wodą i specjalnymi odczynnikami w celu oddzielenia pierwiastków ziem rzadkich od odpadów poflotacyjnych. W zależności od pochodzenia rudy koncentrat może być również poddawany rafinacji elektrolitycznej. Metale ziem rzadkich można rafinować i ekstrahować elektrochemicznie, przez destylację, wymianę jonową lub innymi technikami. Koncentrat (ruda rafinowana) jest następnie wytapiany. Oznacza to, że jest podgrzewany do bardzo wysokich temperatur (~1500°C), dzięki czemu cenne metale można oddzielić od bezużytecznych materiałów w rudzie.
Pierwiastki ziem rzadkich często występują z innymi cennymi metalami, takimi jak metale szlachetne, a w znacznej ilości z metalami nieszlachetnymi, takimi jak miedź i nikiel, dlatego podejmuje się wiele kroków w celu ich oddzielenia.
Proces wyodrębnienia pierwiastków ziem rzadkich jest trudny, ponieważ wiele z nich ma bardzo podobne właściwości, co sprawia, że ich rafinacja jest sporym wyzwaniem. Metody uszlachetniania wymagają użycia drogich chemikaliów i czasochłonnych procesów co wpływa na cenę końcową magnesów neodymowych.
Szacuje się, że około 20-30% neodymu w magnesach neodymowych to tak naprawdę prazeodym (Pr). W rzeczywistości stop używany do produkcji magnesów nazywa się Pr-Nd. Te dwa pierwiastki są chemicznie tak podobne do siebie, że uniemożliwia to ich skuteczne rozdzielenie. Jednocześnie ich podobieństwo powoduje, że wpływ na końcowy produkt, czyli magnes jest niewielki.
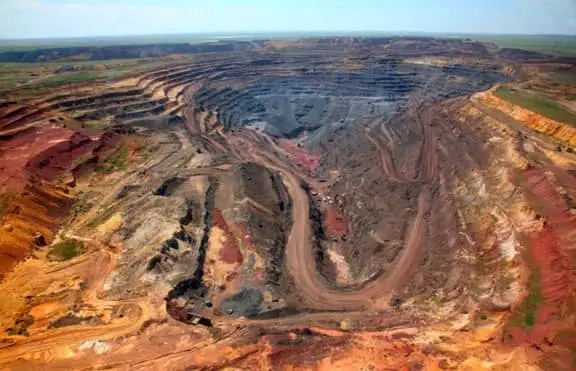
Rys. 2 Kopalnia odkrywkowa
Przygotowanie surowców do stopu
Podczas procesu tworzenia stopu NdFeB wprowadza się do niego niewielkie dodatki innych metali ( Al., Cu, Mo, Nb, W i inne) w celu udoskonalenia i modyfikacji mikrostruktury produktu końcowego. Dodatki stopowe najczęściej nie przekraczają 1% at. powodują zwiększenie koercji magnesu, przy nieznacznym zmniejszeniu remanencji. Bardzo ważnym czynnikiem, który wpływa na jakość późniejszych magnesów jest wielkość cząstek, które powstaną po kruszeniu i rozdrabnianiu stopu. Istnieją dwa sposoby otrzymania proszku ze stopu. Pierwszy sposób to skorzystanie z wlewek stopu. Drugi sposób polega na szybkim chłodzeniu stopu ze stanu ciekłego.
Proszek z wlewek stopu
Po odlaniu stopu do wlewek następuje etap kruszenia mechanicznego. Proces ten jest stosunkowo trudny ze względu na dużą twardość odlewu. Powszechnie stosowana jest metoda rozdrabniania wodorem (HD), która polega na nasyceniu wlewek gazowym H2. Proces ten zachodzi w temperaturze pokojowej i przy ciśnieniu atmosferycznym. Duży wzrost objętości materiału w wyniku absorpcji wodoru prowadzi do jego rozpadu na mniejsze cząstki. Po rozdrobnieniu wstępnym następuje mielenie stopu w młynach kulowych lub strumieniowych do wielkości cząstek ok 3 µm. Proces ten musi być prowadzony w środowisku ochronnym, gazowym lub ciekłym, ze względu na dużą szybkość utleniania materiału. Powstałe cząstki proszku mają nieregularny kształt, a także rozmiar ziaren jest zróżnicowany. Dodatkowo, aby ujednolicić proszek, należy frakcjonować. Idealna byłaby cząstka jednodomenowa o wielkość 0,3 µm, jednak nie jest możliwe osiągnięcie takiego rozmiaru ze względu na duże utlenianie, oraz dużą gęstość defektów strukturalnych. Ostatecznie otrzymywane są cząstki wielodomenowe.
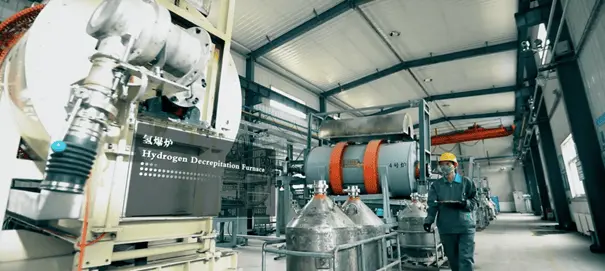
Rys. 3 Urządzenia do rozdrabniania wlewek metodą wodorową HD
Szybkie chłodzenie stopu ze stanu ciekłego
Szybkie chłodzenie jest techniką, polegającą na natryskiwaniu ciekłego, gorącego stopu strumieniem sprężonego gazu na bardzo szybko wirujące, dość dużych rozmiarów miedziane koło. Szybkość chłodzenia z fazy ciekłej do stałej osiąga wartość 105 ̊/s. Szybkość chłodzenia ma istotne znaczenie dla osiągnięcia materiału o bardzo małym ziarnie i może być regulowana prędkością obwodową miedzianego koła. Zbyt szybkie chłodzenie może doprowadzić do powstania struktury amorficznej, co nie jest wskazane. Istnieje odpowiedni zakres parametrów procesu, w którym powstaje odpowiednio mała wielkość ziaren, a występującej śladowej ilości fazy amorficznej można pozbyć się, stosując wyżarzanie. Dla stopów metali z grupy ziem rzadkich łatwo utleniających się, proces ten musi być prowadzony w atmosferze ochronnej.
Tak jak w przypadku otrzymywania proszku z wlewków, tak i w tym sposobie, w dalszej kolejności materiał w celu rozdrobnienia na mniejsze cząstki poddawany jest rozdrabnianiu wodorowemu i mieleniu.
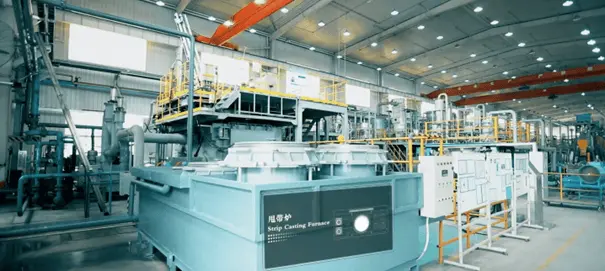
Rys. 4 Piec próżniowy do odlewania taśm ze stanu ciekłego
Prasowanie w polu magnetycznym
Prasowanie w polu magnetycznym ma na celu wytworzenie anizotropowych wyprasek, co pomaga w uzyskaniu wysokiej indukcji remanencji późniejszych magnesów.
Proszek formowany jest przy użyciu pras hydraulicznych. Zazwyczaj stemple górny i dolny prasy są jednocześnie nabiegunnikami elektromagnesu. Prasowanie jest zbliżone do prasowania izostatycznego, jednak nie jest nim w pełni, dlatego mówi się o prasowaniu pseudo-izostatycznym. Taka metoda pozwala zwiększyć gęstość prasowanej wypraski magnesu i jej jednorodność w całej objętości. Ma to ogromny wpływ na końcowe parametry.
Cząstki proszku ustawiają się osiami łatwego magnesowania w kierunku pola magnetycznego, a stopień steksturowania zależy od natężenia pola magnetycznego, oraz udziału objętościowego monokrystalicznych cząstek.
Spiekanie magnesów neodymowych
Proces spiekania przeprowadzany jest w wysokowydajnych piecach, w wysokiej próżni lub atmosferze gazu ochronnego. Optymalna temperatura spiekania jest zależna od składu materiału i wynosi około 1100 ̊C. Czas trwania procesu wynosi od 1 do 3h. Temperatura ustawiana jest na granicy płynięcia wyprasek, co częściowo nawet występuje i ułatwia zagęszczenie spieku. Po procesie spiekania domeny magnetyczne w ziarnach zachowują tą samą orientację, jaką miały po operacji prasowania w polu magnetycznym. Materiał osiąga maksymalną gęstość, a spiekane elementy kurczą się do finalnych rozmiarów. Dodatkowo podczas procesu spiekania zachodzi proces desorpcji wodoru, który jest niewskazany w końcowym produkcie. Początkowo przy temperaturze około 200 ̊C usuwany jest on z fazy Nd2Fe14B, a następnie w temperaturach 250 i 600 ̊C z fazy wysokoneodymowej, występującej na granicach ziaren.
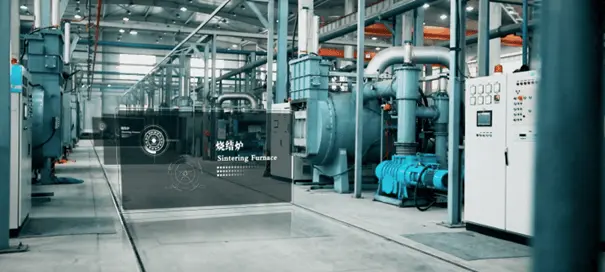
Rys. 5 Piece do spiekania wyprasek
Wyżarzanie magnesów neodymowych
Po spiekaniu, w objętości materiału występują różnego rodzaju naprężenia. Elementy są ponownie poddawane obróbce cieplnej w sposób stopniowy w niższych temperaturach, aby zmniejszyć naprężenia. W zależności od składu chemicznego materiału może być stosowana jedno lub dwustopniowa obróbka cieplna. Przeprowadza się ją w temperaturach 900 i 600 ̊C. Wyżarzanie oprócz pozbycia się naprężeń pozwala na rozpuszczenie niestabilnych, miękkich magnetycznie faz. Po odpowiednim przetrzymaniu w zadanych temperaturach materiał jest powoli chłodzony do temperatury pokojowej.
Obróbka mechaniczna magnesów neodymowych
W kolejnych etapach wytwarzania magnesów neodymowych przygotowuje się zaplanowaną ilość materiału wsadowego, tak aby powstałe później spieki NdFeB miały odpowiednią wielkość wymiarową. Cięcie, obróbka skrawaniem, obróbka elektroerozyjna i szlifowanie odbywa się zgodnie ze ścisłym planem kontroli, aby powstało jak najmniej odpadu. Cięcie jest wykonywane bardzo cienkim drutem, aby zminimalizować straty rzazu. Powstałe odpady są ponownie wykorzystywane i poddawane recyklingowi.
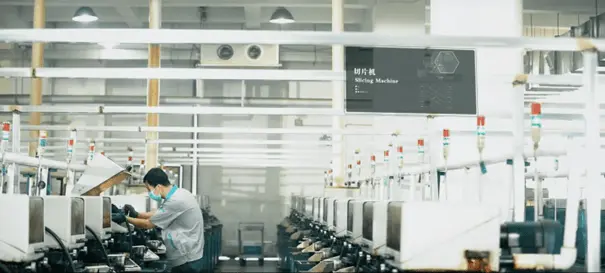
Rys. 6 Przecinarki drutowe
Po obróbce mechanicznej detale posiadają wymagane kształty i wymiary. Końcowym etapem jest nadanie im odpowiedniego wyglądu i zabezpieczenie powłokami. Podstawową warstwą ochronną jest nakładana galwanicznie powłoka niklowo-miedziano-niklowa, która chroni nieznacznie magnes przed korozją w typowych środowiskach użytkowania. Istnieje wiele rodzajów nakładanych warstw, które w zależności od składu mogą mieć różne własności.
Przykładowo powłoka Al-Zn czy Cu zapewnia znacznie lepszą ochronę niż NiCuNi. Powłoka epoksydowa jest bardzo dobrą powłoką do intensywnych środowisk i jest zalecana przez użytkowników końcowych do zastosowań, w których magnesy mogą być narażone na działanie środowisk słonych. Oprócz zabezpieczeń przed korozją stosuje się powłoki typowe dla podniesienia walorów estetycznych, np. warstwy złota, czy cynku pasywującego w kolorze żółtym lub niebieskim.
Magnesowanie magnesów neodymowych
Jednym z ostatnich kroków w produkcji magnesów neodymowych jest ich namagnesowanie. Po wcześniejszych etapach produkcji detale posiadają uprzywilejowane kierunki magnesowania, ponieważ proces prasowania w polu magnetycznym spowodował odpowiedni rozkład i kierunek domen magnetycznych. Do magnesowania wykorzystuje się magneśnice impulsowe. Pozwalają one na wytworzenie w krótkim czasie bardzo dużego pola o indukcji magnetycznej rzędu 5 [T]. Dzięki zastosowaniu tak dużego pola magnetycznego magnesy ulegają nasyceniu. Materiał ferromagnetyczny i rozkład domen powoduje, że nawet po odjęciu zewnętrznego pola magnetycznego magnes zostaje trwale namagnesowany. Wartość pozostałej w magnesie indukcji magnetycznej to indukcja remanencji Br. Jest ona zależna od wszystkich wcześniejszych etapów produkcji magnesów neodymowych.
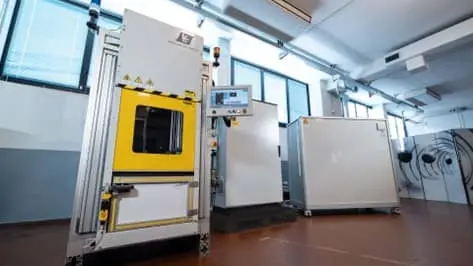
Rys. 7 Magneśnica impulsowa firmy Laboratorio Elettrofisico
Kontrola jakości magnesów neodymowych
Ostatnim krokiem produkcji magnesów neodymowych jest sprawdzenie ich jakości. Należy dodać, że kontrole przeprowadzane są na każdym etapie produkcji, ponieważ mają bardzo duży wpływ na końcowy efekt. Poczynając od początkowych etapów, w przypadku złego oczyszczenia rudy, czy nieodpowiednich doborów składników stopu, dalsze etapy produkcji nie miałyby sensu bez prawidłowej kontroli jakości. Po obróbce mechanicznej detale sprawdzane są pod względem odpowiednich wymiarów i jakości powierzchni. Również po nałożeniu warstw ochronnych są one kontrolowane pod względem grubości i odporności korozyjnej. Na koniec sprawdzane jest to co najistotniejsze dla magnesu, czyli jego parametry magnetyczne. Histerezograf podczas pomiaru magnesu wyznacza krzywą odmagnesowania (II ćwiartkę pętli histerezy magnetycznej), na podstawie której stwierdza się, że parametry magnesu neodymowego są właściwe dla produkowanej klasy magnesów neodymowych.
Po wykonaniu wszystkich powyższych etapów z zachowaniem standardów jakościowych otrzymujemy gotowy produkt – magnes neodymowy.
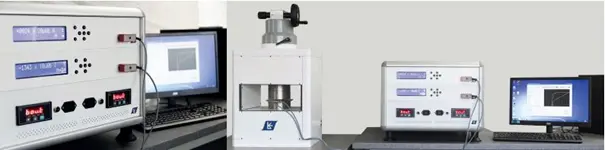
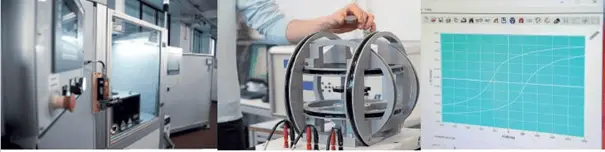
Rys. 8 Kontrola jakości za pomocą histerezografu (w cewce kompensacyjnej) oraz przy pomocy fluksometrów (w cewce Helmholtza)
Inne metody produkcji magnesów neodymowych
Oprócz metod wytwarzania magnesów neodymowych poprzez odlewanie i spiekanie proszków istnieją inne metody pozwalające wytworzyć magnesy o specyficznych właściwościach. Należą do nich:
- - metoda wodorowa HDDR
- - mechaniczna synteza stopów
- - wiązanie proszków spoiwem
1. Metoda wodorowa HDDR (Hydrogenation, Disproportionation, Desorption, Recombination) polega na przemianie gruboziarnistego wlewka w materiał o bardzo rozdrobnionej strukturze, pozwalającej otrzymać magnesy o dużej koercji.
Proces przebiega w atmosferze wodoru w podwyższonej temperaturze. W początkowej fazie prowadzi on do rozpadu materiału na proszek, podobnie jak w metodzie HD. W dalszej części, w zakresie temperatur 750-900 ̊C, dochodzi do rozkładu faz i metaliczny Nd reaguje z Fe i Fe2B tworząc drobnoziarnistą strukturę Nd2Fe14B. Powstały materiał jest izotropowy i wykazuje dużą koercję. Dodatek galu lub cyrkonu do stopu w procesie HDDR powoduje efekt w postaci wprowadzenia anizotropii mikrostruktury.
Proszki otrzymywane metodą HDDR są stosowane do produkcji magnesów wiązanych tworzywem sztucznym zarówno izotropowych, jak i anizotropowych.
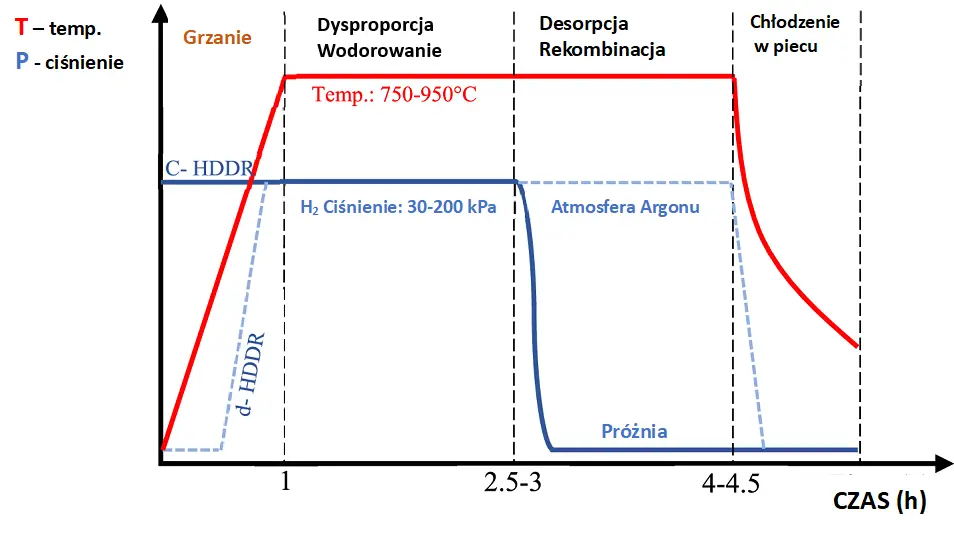
Rys. 9 Schemat procesu HDDR (C-HDDR – konwencjonalny, d-HDDR - dynamiczny)
2. Mechaniczna synteza stopów pozwala na osiągnięcie, podobnie jak przy szybkim chłodzeniu, struktury mikro, a nawet nanokrystalicznej. Proces polega na mieleniu proszku stopu w młynach kulowych, gdzie jest wielokrotnie odkształcany i spajany. Tworzy to charakterystyczną dla tego procesu strukturę warstwową. Z czasem następuje duże rozdrobnienie mikrostruktury o bardzo dużej liczbie defektów. Duże rozdrobnienie powoduje, że w wyniku krótkotrwałego (10 min) wyżarzania w temperaturze 700 ̊C uzyskuje się mikro lub nanostrukturę Nd2Fe14B charakteryzującą się dużą koercją. Wyżarzany proszek może być stosowany do produkcji magnesów wiązanych, można wytworzyć z niego lity magnes izotropowy poprzez prasowanie na gorąco w temperaturze 600 ̊C i ciśnieniu 1000 MPa. Analogicznie, jak przy metodzie szybkiego chłodzenia, powtórne prasowanie pozwala uzyskać materiał anizotropowy, a po jego rozdrobnieniu proszek może być stosowany do magnesów anizotropowych wiązanych tworzywem sztucznym.
3. Wiązanie proszków spoiwem bazuje na połączeniu wcześniej wytworzonego proszku Nd2Fe14B metodami szybkiego chłodzenia czy HDDR z materiałami stanowiącymi osnowę. Najczęściej ze względu na właściwości i sposób obróbki są to tworzywa sztuczne, ale mogą być to także niskotopliwe metale np. Zn. Pierwszą techniką łączenia proszku magnetycznego z tworzywem sztucznym jest mieszanie i prasowanie. Dodatkowo stosowana jest obróbka cieplna np. utwardzanie polimeru w zadanej temperaturze. Zaletą tej metody jest stosunkowo duża zawartość materiału magnetycznego.
Druga metoda produkcji magnesów wiązanych polega na wtrysku mieszaniny proszku magnetycznego i polimeru. Jest ona szybka i umożliwia produkcję masową, lecz wymaga użycia mniejszej ilości materiału magnetycznego co zmniejsza remanencję i gęstość energii magnetycznej. Ze względu na użycie większej ilości materiału wiążącego magnesy powstałe tą metodą mogą być stosowane w wyższej temperaturze. Zastosowanie odpowiednich warunków chłodzenia cieczy pozwala uzyskać taśmę o znacznym stopniu orientacji ziaren. Wymagana mała szybkość chłodzenia sprawia, iż ziarna są duże, co znacznie zmniejsza koercję materiału. Pozwala to jednak na produkcję anizotropowych magnesów wiązanych. Jak wcześniej wspomniano w tej metodzie można zastosować proszek anizotropowy wytwarzany metodą HDDR.
W dalszej części produkcji magnesów neodymowych wiązanych w zależności od właściwości użytkowych stosuje się różne metody obróbki:
- - wytłaczanie
- - prasowanie
- - walcowanie
- - zagęszczanie
Obecnie magnesy neodymowe wiązane produkowane są na szeroką skalę, mimo iż nie posiadają tak wysokich właściwości magnetycznych jak magnesy spiekane. Decyduje o tym niższy koszt wytwarzania, lepsze właściwości antykorozyjne dzięki zastosowaniu osnowy polimerowej, czy też elastyczność i giętkość gotowych wyrobów. Dodatkowo możliwa jest produkcja takich magnesów o bardziej skomplikowanych kształtach w stosunku do magnesów neodymowych spiekanych.
Autor: Wojciech Lisowski